As a business owner or restaurant manager, you're always juggling a dozen tasks, from managing staff to keeping customers happy. But there's one unsung hero in this daily hustle: your inventory.
It's not just about having enough stock; it's about having the right stock. And that's where 'par inventory' shines like a beacon of organization and foresight in the often chaotic world of inventory management.
In this blog, we'll dive deep into the world of par inventory. We'll explore how this simple yet powerful concept can transform the way you handle your stock, from kitchen staples to the trendiest items on your shelf. Let's dive in!
What is par inventory?
Par inventory, in its simplest form, is about maintaining an optimal level of stock that aligns with your average inventory usage. It's like having a secret formula that tells you exactly how much of each inventory item you need to meet customer demand without overstocking and tying up too much cash in unused inventory.
This balancing act is crucial, especially in a restaurant or a small business where every inch of shelf space and every dollar counts.
But why is par inventory so important?
When it comes to restaurant inventory management, excess stock is not just a space eater; it's a cash guzzler. Too much stock can lead to food waste or obsolescence, while too little can mean missed sales opportunities and unhappy customers.
Par inventory strikes a beautiful balance, ensuring you have a safety stock that acts as a cushion against unexpected demand, yet not so much that your storage turns into a museum of forgotten goods.
Calculating PAR levels: a step by step guide
Calculating PAR (Periodic Automatic Replacement) levels might sound like you need a degree in rocket science, but fear not! It’s actually a straightforward process that can significantly boost your inventory management game. Let’s break down this process into digestible steps, so you can start implementing these par level calculations with confidence.
Step 1: Assess Your Average Usage
First things first, you need to understand your average inventory usage. This means diving into your sales data and inventory records. Look at your average weekly usage for each inventory item. How much of each product do you go through in a typical week? This step is crucial for setting a realistic and effective par level.
Step 2: Factor in Delivery Frequency
How often do you restock? Your delivery frequency plays a big role in determining your par levels. If you get deliveries daily, your par levels will be different from a business that restocks weekly. Remember, the goal is to have just enough until your next shipment arrives.
Step 3: Account for Safety Stock
Safety stock is your buffer against the unexpected – like a sudden spike in demand or a delay in delivery. To calculate this, consider factors like historical inventory usage trends and potential unexpected demand. This step helps ensure you’re never caught off guard.
Step 4: The Par Level Formula
Now, for the actual calculation.
Here’s a simple formula:
ParLevel = (Average Usage x Delivery Frequency) + Safety Stock Par Level (Average Usage x Delivery Frequency) + Safety Stock
Plug in your numbers from the previous steps, and voila, you have your par level!
Step 5: Adjust as Needed
Your first calculation might not be perfect, and that’s okay! Effective inventory management involves regular review and adjustments. Keep an eye on how your par levels are working and tweak them based on changing trends or business needs.
Step 6: Implement and Monitor
With your par levels calculated, implement them into your inventory management system. This could be as simple as a par inventory sheet template or as sophisticated as an inventory management software. The key is to monitor and manage these levels consistently to ensure they are serving your business well.
By following these steps, you've not just calculated your par levels; you’ve laid the foundation for a more efficient and responsive inventory management strategy. Next up, we'll explore how to put these calculated par levels into action in your daily operations.
Implementing PAR Inventory: A practical approach
Alright, so you've crunched the numbers and calculated your par levels. Now, it's time to roll up your sleeves and bring these figures to life in your day-to-day operations. Implementing par inventory is like setting the stage for a seamless performance in inventory management. Here’s how to do it effectively:
Step 1: Integrate Par Levels into Your Inventory System
Whether you’re using a sophisticated inventory management solution or a simple par inventory sheet template, the first step is to integrate your newly calculated par levels into your system. This integration allows for a clear view of what needs to be ordered and when. If you're using inventory software, set up alerts or auto-populate purchase orders when stock levels dip below your par level.
Step 2: Train Your Team
A system is only as good as the people using it. Educate your staff about what par levels are and how they impact your business. Ensure that everyone involved in inventory management understands how to read the par inventory sheet or use the inventory management software. This step is crucial for minimizing human error and maintaining accurate inventory records.
Step 3: Regularly Review and Adjust Par Levels
The market isn’t static, and neither should your par levels be. Regularly review your par levels in the context of sales data, customer demand, and inventory turnover rate. Seasons change, trends come and go, and your inventory needs to adapt to these changes. This ongoing process ensures your par levels remain relevant and effective.
Step 4: Optimize Stock Orders
With your par levels set, ordering stock becomes more of a science than a guesswork. Use your par inventory levels as a guide to order just the right amount of inventory. This approach not only helps in maintaining a healthy inventory turnover rate but also reduces the chances of overstocking and understocking.
Step 5: Leverage Technology
If you haven’t already, consider investing in an inventory management system that supports par level management. Many modern systems offer features like real-time tracking, predictive analytics, and automated ordering, which can greatly enhance the efficiency of your par inventory management.
Step 6: Monitor, Evaluate, and Refine
Finally, keep a close eye on how implementing par levels is affecting your business. Look out for improvements in areas like reduced food waste, better cash flow, and increased customer satisfaction. Don’t hesitate to refine your approach as you gain more insights.
By following these practical steps, you're not just implementing a system; you're cultivating a culture of efficiency and foresight in your business's inventory management. Next, let's explore how technology can further enhance this efficiency.
Par Inventory and technology: Enhancing efficiency
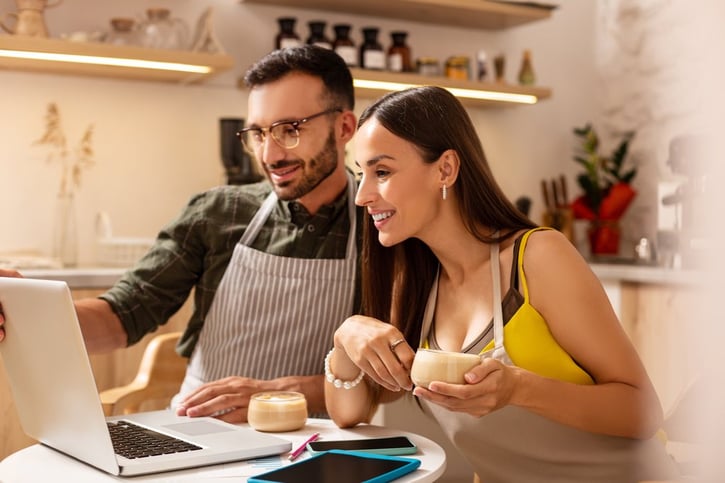
By integrating technology into your par inventory management, you unlock a new realm of efficiency, accuracy, and ease. Let’s explore how technology revolutionizes this crucial aspect of your business.
Embracing Inventory Management Software: Gone are the days of manual counts and guesswork. Inventory management software transforms how you track, manage, and order stock. These systems often come with features that automatically track inventory usage trends, calculate par levels, and even suggest reorder quantities based on historical data. With inventory tracking at your fingertips, you can spend less time counting and more time strategizing.
Real-Time Data Analysis: The beauty of modern inventory management solutions lies in their ability to provide real-time insights. This means you can monitor inventory levels, view sales data, and adjust par levels on the fly. Such timely information is crucial for responding to unexpected demand, managing par levels efficiently, and reducing the risk of stockouts or overstocking.
Automated Ordering Systems: Imagine a system where your inventory orders itself. Sounds futuristic? Well, it’s a reality with today's technology. Some inventory systems can auto-populate purchase orders when stock reaches a certain level, ensuring you always maintain optimal inventory levels. This automation not only saves time but also reduces the risk of human error in ordering processes.
Mobile Accessibility: In a fast-paced business environment, being able to manage inventory on the go is a game-changer. Many inventory management software options offer mobile device compatibility, allowing you to manage par levels, place orders, and track inventory from anywhere. This flexibility is especially beneficial for restaurant managers and small business owners who are constantly on the move.
Integrating with Other Systems: For a holistic approach, integrating your inventory management system with other business systems, like point-of-sale (POS) and accounting software, can provide comprehensive insights. This integration enables a seamless flow of information, making it easier to track sales data, manage stock levels, and understand your business’s financial health in relation to inventory.
Analytics and Predictive Tools: Advanced inventory management solutions offer analytics and predictive tools that go beyond just tracking stock levels. These tools can analyze trends, predict future demand, and even suggest optimal par levels based on seasonal changes or market trends. This level of insight is invaluable for making informed decisions and staying ahead in the game.
By harnessing the power of technology in par inventory management, you're not just keeping up with the times; you're setting your business up for streamlined operations, reduced costs, and enhanced customer satisfaction.
Conclusion
As we wrap up this blog post, it's clear that mastering this aspect of inventory management is more than just a business practice; it's a strategic move towards sustainability and profitability.
Whether you're running a cozy corner café or a bustling restaurant, the principles of par inventory are universal, offering a beacon of efficiency in the often turbulent waters of inventory management.
Embracing par inventory isn't just about staying organized; it's about staying ahead. It's a commitment to understanding your business's heartbeat – the ebb and flow of customer demand, the rhythm of your sales data, and the melody of your stock levels.
By fine-tuning your par levels and leveraging technology, you're not just managing inventory; you're choreographing a dance that aligns perfectly with the unique tempo of your business.
Let's not forget that at the heart of every successful business is a well-oiled inventory system. Par inventory, with its focus on balance and foresight, stands as a testament to the power of smart inventory management.
Implement it with care, embrace the technological aids available, and watch as it transforms the efficiency and effectiveness of your business operations.